IDDO sends new ice coring drill to Greenland
Having designed and built what will be the nation’s next generation of ice coring drills, the Ice Drilling Design and Operations group (IDDO) at the University of Wisconsin-Madison’s Space Science and Engineering Center will send its instrument packing for Greenland March 26.
The drill is called IDD, for Intermediate Depth Drill, since it is designed to recover ice cores from depths of 1,500 meters—nearly 5,000 feet—which is less than half the length of the longest ice core ever recovered by the U.S., a record set by the IDDO team in 2012.
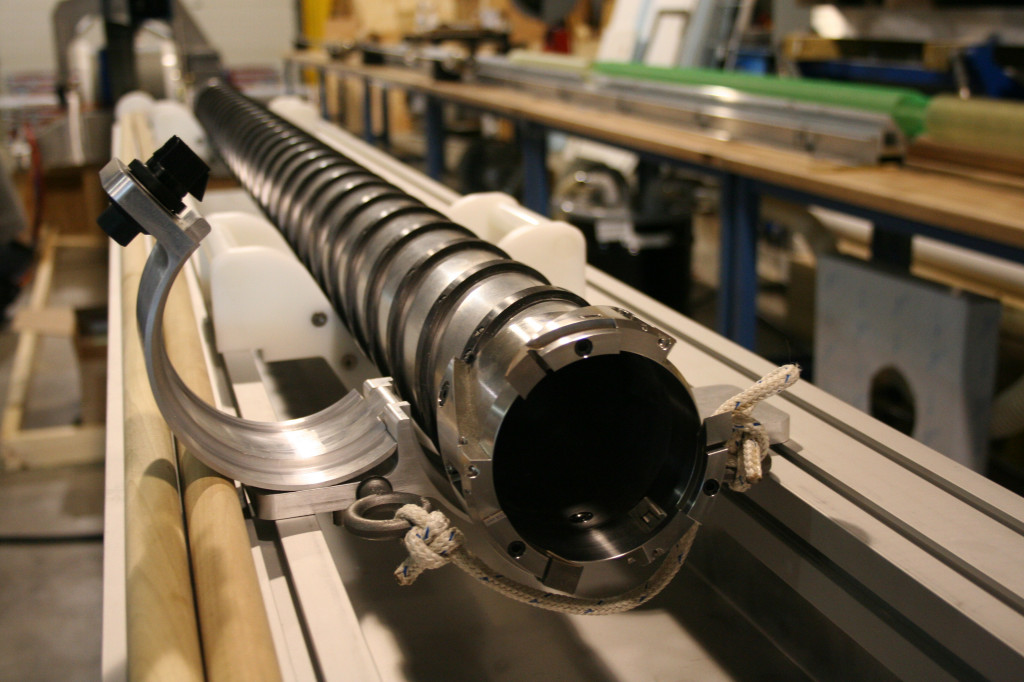
The Intermediate Depth Drill (IDD) will be able to recover ice cores almost 5,000 feet deep. Photo credit: Sarah Witman, SSEC.
Ice coring drills provide scientists with ice samples thousands of years old, from which they can learn about changes in climate and air quality over time. Traces of chemicals and isotopes within the ice tell stories about the Earth and its history. For example, ice core records were central to the discovery that climate can change dramatically and abruptly, sometimes over periods less than 10 years.
The higher the quality of each ice core—smooth, frozen cylinders with minimal cracks and breaks—the more researchers will be able to learn. So, a well constructed ice coring drill is key.
The National Science Foundation contracted with IDDO to build IDD in 2011, the same year the group completed its last drill—the Deep Ice Sheet Coring (DISC) Drill with replicate coring capability.
Shipping the IDD to Greenland for testing, and to its eventual home at the South Pole, will be a carefully orchestrated event.
The drill, accompanied by three IDDO personnel and as many contractors, deploys March 26, taking a four-engine military transport aircraft from Schenectady, NY, to Summit Station, the year-round research camp in Greenland. There, the team will test IDD by drilling up to 600 meters into the surface of the ice.
In June, following successful testing in Greenland, the team will return to Madison for two months before shipping IDD by boat to New Zealand. The drill is scheduled to reach its final destination, Antarctica’s South Pole Station, in late November.
Fortunately, all the components of the drill can be transported in one flight, instead of nine-plus, as was the case with the DISC drill.
“The IDD has been designed so it can be transported by small aircraft,” said Jay Johnson, Drill Operations Engineer for IDDO and lead engineer for IDD. “Individual components of the drill can be moved by four people and assembled with hand tools; you don’t need heavy equipment. We designed it to be small, light and break down well, which will help the drill to be practical for coring at a wide variety of locations.”
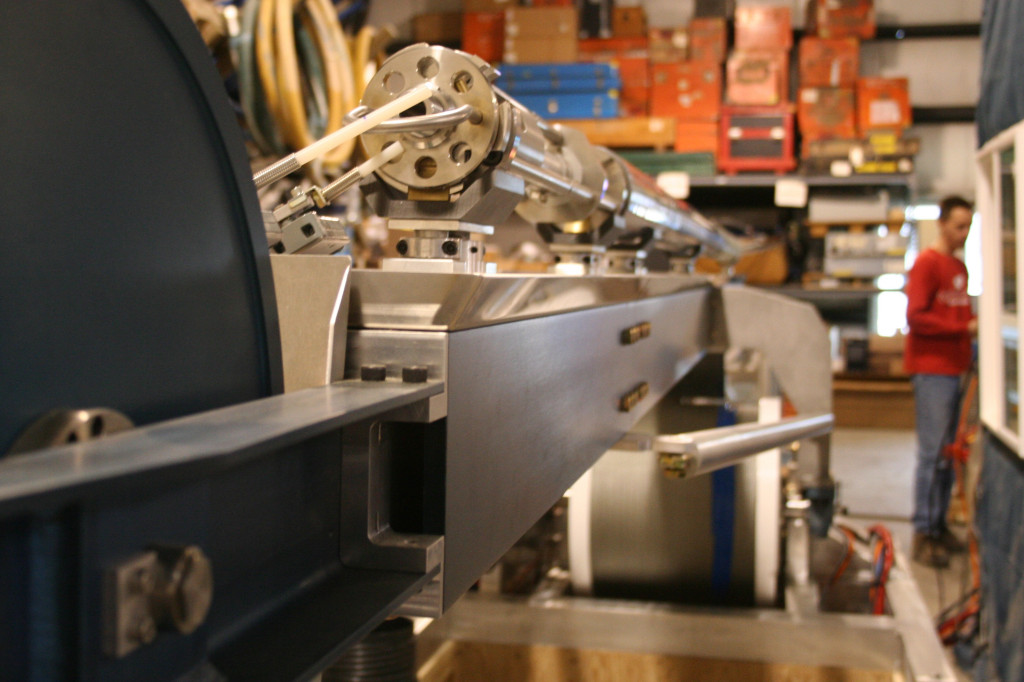
The barrel of the IDD ice coring drill with its lead engineer, Jay Johnson, in the background. Photo credit: Sarah Witman, SSEC.
Mobility was not the only criteria that IDD’s engineers kept in mind: The drill needs to be fully functional at -57 degrees Celsius, or -71 degrees Fahrenheit. Even in Wisconsin, where temperatures easily drop below 20 degrees Fahrenheit each winter, designing equipment for the harsh Antarctic climate was a major challenge. Selecting the right materials for the various drill components was critical because some materials that remain pliant and sturdy at room temperature can fail or become brittle at this temperature. One bonus, though, is that waste-heat from the drill’s winch motor will be applied to heat the crew’s workspace and save energy.
Working in an environment such as the South Pole is ideal as ice is constantly being formed. Snow falls to the Earth’s surface, and, as it accumulates, it gains more weight, compressing everything below into ice.
“The deeper you go, the more ductile the ice is,” explained IDDO Engineering and Research Director and IDD project manager Alex Shturmakov. “After the coring drill passes the brittle zone, it becomes much easier to recover a high quality ice core.”
Ice coring drills such as the IDD function something like a cross between a drinking straw, cookie-cutter and corkscrew—with a lot more power. Powered by an electric motor, the long, hollow barrel of the drill spins at a constant speed of about 60 rpm, using its sharp, metallic cutting head to carve out two-meters-long ice cores.
The ice cores that IDD will extract will be 98 millimeters (about 4 inches) across, a new core diameter for the team.
After the ice cores are drilled, they will be transported to the National Ice Core Lab (NICL) in Denver, CO, for initial analysis, cataloging and storage. From there, samples will be distributed to scientists for further study.
“They like the cores to be stored at below -20 degrees Celsius. Part of the core will be kept on site at the South Pole for a year, to let the ice relax, so the cores aren’t damaged in transport,” Shturmakov said.
The drill will be used for the South Pole Ice Core project during the 2014-2015 and 2015-2016 seasons in Antarctica, while proposals for future drilling sites are being planned.
Shturmakov said he feels grateful for all the support IDDO has received from various departments at UW Space Science and Engineering Center, as well as other organizations in the U.S. and from Denmark and New Zealand.
by Sarah Witman